8d-methode (qualität)
In diesem Artikel wird erklärt, was die 8D-Methode ist und wofür sie verwendet wird. So erfahren Sie, was die acht Schritte der 8D-Methode sind, ein Beispiel für ihre Anwendung und welche Vorteile die Implementierung dieser Methodik in der Wirtschaft bietet.
Was ist die 8D-Methode?
Die 8D-Methode , auch Acht Disziplinen der Problemlösung genannt, ist ein Modell zur Lösung von Qualitätsmanagementproblemen. Die 8D-Methode umfasst acht Schritte, die befolgt werden müssen, um das Problem zu lösen, zu beheben und seine Ursache zu beseitigen.
Somit basiert die 8D-Methode auf der Anwendung dauerhafter Korrekturmaßnahmen, die auf der statistischen Analyse des Problems und der Ursache des Problems durch Ermittlung der Grundursachen basieren.
Die 8D-Methode wird auch unter anderen Namen wie 8-D Problem Solving , G8D oder Global 8D bezeichnet.
Die 8D-Qualitätsproblemlösungsmethode wurde 1987 vom Automobilhersteller Ford erfunden. Das Unternehmen nannte diese Methodik damals G8D oder Global 8D. Derzeit wird die 8D-Methode nicht nur von Unternehmen der Automobilbranche, sondern auch in anderen Branchen zur Lösung von Problemen im Zusammenhang mit dem Qualitätsmanagement eingesetzt.
Die 8D-Methode ähnelt der PDCA-Methode darin, dass beide ein Verfahren zur Lösung eines Problems und zur Verbesserung der Qualität eines Produkts, Prozesses oder einer Dienstleistung bereitstellen. Die Ähnlichkeiten und Unterschiede zwischen diesen beiden Methoden können Sie hier sehen:
Was sind 8Ds?
Im Qualitätsmanagement sind die acht Disziplinen der 8D-Methode:
- D1: Bilden Sie ein Team.
- D2: Definieren Sie das Problem.
- D3: Führen Sie eine vorübergehende Eindämmungsmaßnahme durch.
- D4: Identifizieren Sie die Grundursache.
- D5: Legt Korrekturmaßnahmen fest.
- D6: Permanente Korrekturmaßnahmen umsetzen.
- D7: Verhindern Sie, dass ein ähnliches Problem erneut auftritt.
- D8: Anerkennung der Bemühungen des Teams.
Hinweis: Obwohl die 8D-Methode ursprünglich aus acht Schritten bestand, fügen einige Qualitätsexperten jetzt einen ersten Schritt mit der Bezeichnung „Notfallvorsorge und Reaktionsmaßnahmen“ hinzu.
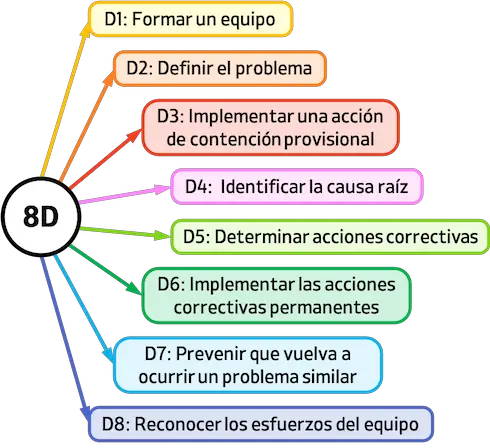
Bilden Sie ein Team
Das Team muss multidisziplinär sein und über Erfahrung mit dem untersuchten Produkt, Prozess oder der untersuchten Dienstleistung verfügen. Wenn es ein Problem mit einem Produkt gibt, ist es wichtig, die Bedürfnisse des Kunden zu verstehen. Daher ist es hilfreich, einen Marketingmitarbeiter oder sogar einen Kunden im Team zu haben. Auch wenn Prozesse und Personal sich ändern müssen, kann es hilfreich sein, einen Personalvertreter im Team zu haben.
8D-Teams sollten zwei Schlüsselmitglieder haben:
- Leiter: ist die Person, die den 8D-Prozess kennt und das Team durch ihn führen kann (auch wenn es nicht immer die Person ist, die am besten über das zu untersuchende Problem Bescheid weiß).
- Champion : ist die Person, die die endgültige Genehmigung der mithilfe der 8D-Methodik umzusetzenden Änderungen erteilen kann.
definiere das Problem
Das Problem muss mithilfe quantifizierbarer Begriffe definiert werden. Die Beschwerde des Kunden könnte lauten: „Dieses Produkt funktioniert nicht!“ » aber intern muss die Organisation das Problem präzise und numerisch beschreiben.
Um das Problem zu definieren, müssen möglicherweise Testmethoden und Datenerfassung festgelegt, Kunden befragt oder mit Mitarbeitern gesprochen werden, die an der Herstellung des Produkts beteiligt sind.
Zu diesem Zeitpunkt sucht das Team nicht nach der Ursache des Problems, sondern sammelt möglichst viele Informationen, um die Merkmale des Problems zu bestimmen.
Führen Sie vorübergehende Eindämmungsmaßnahmen durch
Wenn das Problem Kunden betrifft, die Produktivität oder die Kosten beeinträchtigt oder ein Gesundheits- oder Umweltrisiko darstellt, muss es sofort behoben werden. Eine Übergangslösung muss identifiziert, bewertet und umgesetzt werden.
Wenn eine vorübergehende Lösung nicht möglich ist, muss der problematische Prozess gestoppt oder geschlossen werden.
Bedenken Sie, dass eine Übergangslösung nicht ohne vorherige Evaluierung umgesetzt werden sollte. Das Team muss sicherstellen, dass die Problemumgehung sicher ist, das aktuelle Problem tatsächlich löst und einfach und kostengünstig zu implementieren ist, ohne neue Probleme zu verursachen.
Identifizieren Sie die Grundursache
Sobald die Problemumgehung vorhanden ist, besteht der nächste Schritt darin, die Grundursache des Problems zu ermitteln. Das übergeordnete Ziel der 8D-Methode besteht darin, das Problem dauerhaft zu beseitigen. Dies kann nur erreicht werden, wenn die Grundursache identifiziert und beseitigt wird.
Die folgenden Tools können in dieser Phase hilfreich sein:
Bestimmt Korrekturmaßnahmen
Sobald wir die Grundursache des Problems kennen, müssen wir Maßnahmen finden und umsetzen, die das Problem lösen. Es ist wichtig, dass Korrekturmaßnahmen die Grundursache des Problems angehen, denn wenn die wahre Ursache des Problems nicht behoben wird, tritt das Problem erneut auf.
Eine der besten Möglichkeiten, eine Lösung zu testen, besteht darin, sie in kleinem Maßstab zu implementieren und zu überwachen, was passiert. Wenn beispielsweise ein Fertigungsprozess mehrere Zellen umfasst, kann die Lösung in einer einzelnen Zelle implementiert und anschließend die erzielten Ergebnisse gemessen werden. Wenn die Lösung in einer Zelle erfolgreich ist, kann sie anschließend in allen Zellen umgesetzt werden.
Implementieren Sie permanente Korrekturmaßnahmen
Sobald die Lösung verifiziert ist, also nachweislich die Grundursache beseitigt, ohne neue Probleme zu schaffen, kann sie durch dauerhafte Maßnahmen vollständig umgesetzt werden.
Um dauerhafte Veränderungen erfolgreich umzusetzen, ist es wichtig zu planen, wie die Veränderung umgesetzt wird. Der Projektplan sollte Folgendes abdecken: Wie wird die Änderung allen Beteiligten kommuniziert, welche Maßnahmen müssen ergriffen werden und wie wird die Änderung überwacht?
Verhindern Sie, dass ein ähnliches Problem erneut auftritt
Eine vollständige Lösung von Problemen bedeutet, zu verhindern, dass sie erneut auftreten. Gemäß der 8D-Methode sollten daher vorbeugende Maßnahmen umgesetzt werden, um zu verhindern, dass das Problem erneut auftritt. Dazu gehört die Überprüfung von Managementprozessen, Betriebsabläufen und Schulungshandbüchern, um sicherzustellen, dass Best Practices befolgt werden.
In dieser Phase sollten Organisationen Maßnahmen in Betracht ziehen, einschließlich der Aktualisierung von Prozessauditfragen und deren regelmäßiger Überprüfung anhand von Korrekturmaßnahmen, um Risiken in anderen Prozessen zu reduzieren.
Eine weit verbreitete Methode zur Vermeidung von Problemen ist Poka-Yoke. In manchen Fällen kann es jedoch schwierig sein, diese Methode anzuwenden. Sie können sehen, was ein Poka-Yoke ist, indem Sie auf den folgenden Link klicken:
Teamleistungen anerkennen
Die Anerkennung von Teamleistungen ist der letzte Schritt der 8D-Methode. Es kann so einfach sein wie ein „Dankeschön“, aber es sollte so erfolgen, dass andere in Ihrer Organisation wissen, was getan wurde. Dies erhöht die Zufriedenheit und Motivation der Menschen, die Teil des Teams waren und hart an der Lösung des Problems gearbeitet haben.
Eine übliche Art, sich zu bedanken, ist ein Artikel im Unternehmensnewsletter oder ein Banner auf den Schwarzen Brettern der Einrichtung. Stellen Sie sicher, dass alle Teammitglieder namentlich genannt werden, damit jeder als Teil des Teams erkannt wird.
Beispiel für die 8D-Methode
Nachdem wir die Theorie zur 8D-Methode kennengelernt haben, sehen wir uns ein Beispiel für die Anwendung der 8D-Methode zur Lösung eines Qualitätsproblems eines Industrieunternehmens an.
Eine Organisation erhielt Beschwerden von Kunden bezüglich der Schrumpfung eines Autoteils. Das Management erforderte eine eingehende Analyse auf Basis der 8D-Problemlösungsmethodik. Der gesendete 8D-Bericht lautete wie folgt:
- D1: Es wird ein Team mit den Mitgliedern des Beschaffungsteams, dem Teamleiter und dem Manager gebildet.
- D2: Zur Beschreibung des Problems dient eine Kundenbeschwerde. Das Problem wird durch die Beantwortung der folgenden Fragen ermittelt:
- Was ist die Beschwerde? Kontraktion im Waschbecken.
- Wann ist es passiert? In der letzten Charge.
- Warum ist das passiert? Aufgrund eines Defekts im Eingabefeld.
- Wer hat das Problem gemeldet? Ein Endkunde.
- Um welche Produktion handelt es sich? 2 % der Gesamtproduktion.
- D3: Als Eindämmungsmaßnahme beschließt das Team, den Versand einzustellen und die guten Teile sofort zu trennen.
- D4: Um die Grundursache zu identifizieren, verwendet das Team die 5-Warum-Methodik:
- Warum haben sie sich beschwert? Durch eine Kontraktion in der Eintrittszone.
- Warum gab es im Eingangsbereich eine Verengung? Denn es wurden hohe Gießtemperaturen verwendet.
- Warum wurden hohe Gießtemperaturen verwendet? Weil der Pyrometerwert falsch war.
- Warum war der Pyrometerwert falsch? Denn der Zustand des Pyrometers wurde nicht überprüft.
- Warum wurde das Pyrometer nicht überprüft? Man kommt zu dem Schluss, dass die Hauptursache des Problems darin liegt, dass sich das Pyrometer in einem schlechten Zustand befand.
- D5: Als permanenter Korrekturplan wird empfohlen, dass der Wartungsleiter das Pyrometer regelmäßig überprüft.
- D6: Es werden permanente Korrekturmaßnahmen umgesetzt und wöchentliche Kontrollen geplant.
- D7: Regelmäßige Inspektionen und ordnungsgemäße Wartung von Pyrometern sind Maßnahmen, um ein erneutes Auftreten des Problems zu verhindern.
- D8: Teamleistung wird anerkannt. Der Manager und das Team werden für die Lösung des Problems gelobt.
Wann ist die 8D-Methode anzuwenden?
Typischerweise wird die 8D-Methode zur Problemlösung verwendet, wenn eine der folgenden Situationen eintritt:
- Wenn sicherheitsrelevante Probleme entdeckt werden oder die Vorschriften oder Regeln nicht eingehalten werden.
- Wenn Kundenbeschwerden eingehen. Im vorherigen Abschnitt sehen Sie ein Beispiel, wie Sie die 8D-Methode in diesem Fall implementieren.
- Wenn Warnungen eingehen, die darauf hinweisen, dass die Produktausfallrate höher als erwartet ist.
- Wenn Produkte die interne Qualitätsprüfung häufig nicht bestehen, werden zu viele Einheiten weggeworfen oder die Produkt- oder Serviceleistung ist sehr schlecht.
Vorteile der 8D-Methode
Die Implementierung der 8D-Methode im Qualitätsmanagement hat folgende Vorteile:
- Es bietet ein einfaches Verfahren zur Behebung eines Problems und zur Ermittlung seiner Grundursache.
- Dies hilft dabei, eine Lösung für das Problem zu finden und diese erfolgreich umzusetzen, sodass das Problem nicht erneut auftritt.
- Dies macht es einfacher, Steuerungssysteme zu finden, die das Problem nicht erkannt haben und daher verbessert werden müssen.
- Logischerweise verbessert sich dadurch die Qualität des Produkts oder der Dienstleistung, was indirekt zu einer höheren Kundenzufriedenheit führt.
- Dies fördert die Teamarbeit, da die Mitarbeiter, aus denen das Team besteht, zusammenarbeiten müssen, um das Problem zu lösen.