8d方式(品質)
この記事では、8D 手法とは何か、またそれが何に使用されるのかについて説明します。したがって、8D 手法の 8 つのステップとは何か、その応用例、そしてこの手法をビジネスに導入する利点は何かを理解することができます。
8D方式とは何ですか?
8D メソッド は、問題解決の 8 つの規律とも呼ばれ、品質管理の問題を解決するために使用されるモデルです。 8D メソッドには、問題を解決し、修正し、原因を取り除くために従う必要がある 8 つのステップが含まれています。
したがって、8D メソッドは、根本原因を特定することによる問題と問題の原因の統計分析に基づく恒久的な是正措置の適用に基づいています。
8D メソッドは、 8-D 問題解決、 G8D 、またはGlobal 8Dなどの別名でも呼ばれます。
8D 品質問題解決手法は、1987 年に自動車メーカーのフォードによって発明されました。当時、同社はこの手法を G8D または Global 8D と呼んでいました。現在、8D 手法は自動車分野の企業だけでなく、他の業界でも品質管理に関する問題を解決するために使用されています。
8D メソッドは、問題を解決し、製品、プロセス、またはサービスの品質を向上させるための手順を提供するという点で PDCA メソッドに似ています。これら 2 つの方法論の類似点と相違点をここで確認できます。
8Dとは何ですか?
品質管理における 8D メソッドの 8 つの分野は次のとおりです。
- D1:チームを結成します。
- D2:問題を定義します。
- D3:一時的な封じ込めアクションを実施します。
- D4:根本原因を特定します。
- D5:是正措置を決定します。
- D6:恒久的な是正措置を実施する。
- D7:同様の問題の再発を防止します。
- D8:チームの努力を称える。
注: 8D メソッドには当初 8 つのステップがありましたが、一部の品質専門家は現在、 緊急時の準備と対応アクション と呼ばれる最初のステップを追加しています。
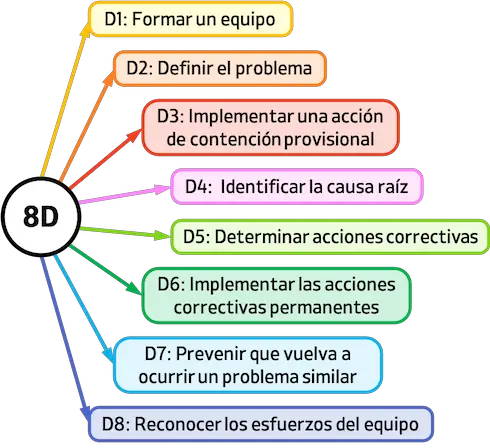
チームを作る
チームは学際的であり、研究対象の製品、プロセス、またはサービスの経験が含まれている必要があります。製品に問題がある場合、顧客のニーズを理解することが不可欠です。したがって、チームにマーケティング担当者、さらには顧客がいると役に立ちます。同様に、プロセスや人員を変更する必要がある場合、チームに人事担当者を置くと役立つ場合があります。
8D チームには 2 人の主要メンバーが必要です。
- リーダー: 8D プロセスを知っており、それを通してチームを導くことができる人です (調査対象の問題について常に最もよく知っている人であるとは限らない場合でも)。
- Champion : 8D 手法を使用して実装される変更の最終承認を与えることができる人物です。
問題を定義する
問題は定量化可能な用語を使用して定義する必要があります。顧客の苦情は、「この製品は動作しません!」である可能性があります。 » しかし、内部的には、組織は問題を正確かつ数値的に説明する必要があります。
問題を定義するには、テスト方法とデータ収集の確立、顧客へのインタビュー、または製品の製造に携わる従業員との会話が必要になる場合があります。
現時点では、チームは問題の原因を探すのではなく、問題の特徴を判断するためにできるだけ多くの情報を収集します。
一時的な封じ込め措置を講じる
問題が顧客に影響を与える場合、生産性やコストに影響を与える場合、あるいは健康や環境リスクを引き起こす場合には、直ちに解決する必要があります。一時的な解決策を特定、評価、実装する必要があります。
一時的な解決策が実現できない場合は、問題のあるプロセスを停止または終了する必要があります。
一時的な解決策は、事前の評価なしに実装すべきではないことに留意してください。チームは、回避策が安全であり、現在の問題を実際に解決し、新たな問題を引き起こすことなく実装が簡単でコスト効率が高いことを確認する必要があります。
根本原因を特定する
回避策が講じられたら、次のステップは問題の根本原因を特定することです。 8D メソッドの全体的な目標は問題を永久に除去することであり、これは根本原因が特定され除去された場合にのみ可能になります。
この段階では、次のツールが役立つ場合があります。
是正措置を決定する
問題の根本原因がわかったら、問題を解決するアクションを見つけて実装する必要があります。問題の真の原因に対処しないと問題が再発するため、問題の根本原因に対処する修正措置が重要です。
ソリューションをテストする最良の方法の 1 つは、ソリューションを小規模に実装し、何が起こるかを監視することです。たとえば、製造プロセスに複数のセルが含まれる場合、ソリューションを単一のセルに実装して、得られた結果を測定できます。 1 つのセルでソリューションが成功した場合は、すべてのセルにそのソリューションを実装できます。
恒久的な是正措置を実施する
解決策が検証されると、つまり、新たな問題を引き起こすことなく根本原因を取り除くことが証明されたら、恒久的な対策を講じることで完全に実行できます。
永続的な変更を成功裏に実装するには、変更をどのように実装するかを計画することが不可欠です。プロジェクト計画には、変更を関係者全員にどのように伝えるか、どのようなアクションを実行する必要があるか、変更をどのように監視するかが含まれている必要があります。
同様の問題の再発を防止する
問題の完全な解決とは、問題の再発を防ぐことを意味します。したがって、8D メソッドによれば、問題の再発を防ぐために予防措置を講じる必要があります。これには、管理プロセス、運用手順、トレーニング マニュアルを見直して、ベスト プラクティスに従っていることを確認することが含まれます。
この段階で、組織は他のプロセスのリスクを軽減するために、プロセス監査の質問を更新したり、修正措置と定期的に照合したりするなどの措置を検討する必要があります。
問題の発生を防ぐために広く使用されている方法はポカヨケですが、場合によってはこの方法論を適用することが難しい場合があります。次のリンクをクリックすると、ポカヨケが何であるかを確認できます。
チームの努力を評価する
チームの成果を評価することは、8D メソッドの最終ステップです。 「ありがとう」のような簡単な言葉でもかまいませんが、組織内の他の人が何が行われたのかわかるようにする必要があります。これにより、チームの一員として問題の解決策を見つけるために一生懸命働いた人々の満足度とモチベーションが高まります。
社内報の記事や施設の掲示板のバナーなどで感謝の気持ちを伝えるのが一般的です。全員がチームの一員として認識されるように、チーム メンバー全員に名前が付けられていることを確認してください。
8D方式の例
8D メソッドの理論を見た後、工業企業の品質問題を解決する 8D メソッドの適用例を見ていきます。
ある組織は、自動車部品の収縮に関する顧客からの苦情を受けました。管理には、8D の問題解決方法論に基づいた詳細な分析が必要でした。送信された 8D レポートは次のとおりです。
- D1:調達チームのメンバー、チームリーダー、マネージャーでチームを編成します。
- D2:顧客からの苦情は問題を説明するために使用されます。この問題は、次の質問に答えることで確立されます。
- 苦情は何ですか?シンク内の収縮。
- それはいつ起きましたか?最後のバッチで。
- なぜこのようなことが起こったのでしょうか?入力ボックスの不具合が原因です。
- 誰が問題を報告しましたか?最終顧客。
- 関係するプロダクションは何ですか?全生産量の2%。
- D3:封じ込め対策として、チームは出荷を停止し、良品部品を直ちに分離することを決定しました。
- D4:根本原因を特定するために、チームは 5 なぜを使用します。
- なぜ彼らは苦情を言ったのでしょうか?エントリーゾーンの収縮により。
- なぜ入口付近に狭さがあったのでしょうか?高い鋳造温度が使用されたためです。
- なぜ高い鋳造温度が使用されたのでしょうか?高温計の測定値が間違っていたからです。
- 高温計の測定値が間違っていたのはなぜですか?高温計の状態を確認していないためです。
- なぜ高温計がチェックされなかったのですか?問題の根本原因は高温計の状態が悪かったことであると結論付けられました。
- D5:恒久的な是正計画として、保守監督者がパイロメーターを定期的に改訂することが提案されます。
- D6:恒久的な是正措置が実施され、毎週のチェックがスケジュールされます。
- D7:パイロメーターの定期的な検査と適切なメンテナンスは、問題の再発を防止するための措置です。
- D8:チームの努力が認められます。マネージャーとチームは問題を解決したことで表彰されます。
8D 手法をいつ適用するか?
通常、8D の問題解決手法は、次のいずれかの状況が発生した場合に使用されます。
- セキュリティ関連の問題が発見された場合、または規制や規則に準拠していない問題が発見された場合。
- お客様から苦情が寄せられた場合。前のセクションでは、この場合の 8D メソッドの実装方法の例を示しました。
- 製品の故障率が予想よりも高いことを示すアラートを受信した場合。
- 製品が内部品質テストに合格しない場合、多くのユニットが廃棄されたり、製品やサービスのパフォーマンスが非常に低下したりすることがあります。
8D法のメリット
品質管理に 8D 手法を導入すると、次のような利点があります。
- 問題のトラブルシューティングを行い、根本原因を見つけるための簡単な手順を提供します。
- これは、問題の解決策を見つけてそれを適切に実装し、問題が再び発生しないようにするのに役立ちます。
- これにより、問題を検出できず、改善が必要な制御システムを簡単に見つけることができます。
- 論理的には、これにより製品またはサービスの品質が向上し、間接的に顧客満足度の向上につながります。
- チームを構成する従業員は問題を解決するために協力する必要があるため、これによりチームワークが促進されます。