วิธี 8d (คุณภาพ)
บทความนี้จะอธิบายว่าวิธี 8D คืออะไร และใช้เพื่ออะไร ดังนั้น คุณจะค้นพบว่าแปดขั้นตอนของวิธี 8D คืออะไร ตัวอย่างการใช้งาน และข้อดีของการใช้วิธีการนี้ในธุรกิจคืออะไร
วิธี 8D คืออะไร?
วิธี 8D หรือที่เรียกว่า Eight Disciplines of Problem Solving เป็นแบบจำลองที่ใช้ในการแก้ไขปัญหาการจัดการคุณภาพ วิธี 8D ประกอบด้วยแปดขั้นตอนที่ต้องปฏิบัติตามเพื่อแก้ไขปัญหา แก้ไข และขจัดสาเหตุของปัญหา
ดังนั้นวิธี 8D จึงขึ้นอยู่กับการประยุกต์ใช้การดำเนินการแก้ไขอย่างถาวรโดยอาศัยการวิเคราะห์ทางสถิติของปัญหาและที่มาของปัญหาโดยการระบุสาเหตุที่แท้จริง
วิธี 8D มีชื่อเรียกอื่นๆ เช่น 8-D Problem Solving , G8D หรือ Global 8D
วิธีแก้ไขปัญหาคุณภาพ 8D ถูกคิดค้นโดยผู้ผลิตรถยนต์ Ford ในปี 1987 ในขณะนั้น บริษัทเรียกวิธีการนี้ว่า G8D หรือ Global 8D ในปัจจุบัน วิธีการ 8D ไม่เพียงแต่บริษัทในภาคยานยนต์เท่านั้น แต่ยังใช้ในอุตสาหกรรมอื่นๆ เพื่อแก้ไขปัญหาที่เกี่ยวข้องกับการจัดการคุณภาพอีกด้วย
วิธี 8D มีความคล้ายคลึงกับวิธี PDCA ตรงที่เป็นทั้งขั้นตอนในการแก้ปัญหาและปรับปรุงคุณภาพของผลิตภัณฑ์ กระบวนการ หรือบริการ คุณสามารถดูความเหมือนและความแตกต่างระหว่างวิธีการทั้งสองนี้ได้ที่นี่:
8D คืออะไร?
ในการจัดการคุณภาพ วิธี 8D มี 8 สาขาวิชา ได้แก่
- D1: จัดตั้งทีม
- D2: กำหนดปัญหา
- D3: ดำเนินการกักกันชั่วคราว
- D4: ระบุสาเหตุที่แท้จริง
- D5: กำหนดการดำเนินการแก้ไข
- D6: ดำเนินการแก้ไขอย่างถาวร
- D7: ป้องกันไม่ให้ปัญหาที่คล้ายกันเกิดขึ้นอีก
- D8: ตระหนักถึงความพยายามของทีม
หมายเหตุ: แม้ว่าวิธี 8D ในตอนแรกจะมีแปดขั้นตอน แต่ผู้เชี่ยวชาญด้านคุณภาพบางคนได้เพิ่มขั้นตอนเริ่มต้นที่เรียกว่า การเตรียมความพร้อมในกรณีฉุกเฉินและการดำเนินการตอบสนอง
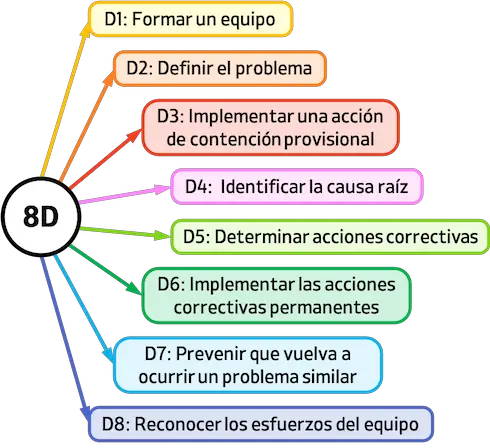
สร้างทีม
ทีมงานจะต้องมาจากหลากหลายสาขาวิชาและมีประสบการณ์ในผลิตภัณฑ์ กระบวนการ หรือบริการที่กำลังศึกษาอยู่ หากเกิดปัญหากับผลิตภัณฑ์ จำเป็นต้องเข้าใจความต้องการของลูกค้า ดังนั้นการมีตัวแทนการตลาดหรือแม้แต่ลูกค้าอยู่ในทีมจึงช่วยได้ ในทำนองเดียวกัน เมื่อกระบวนการและบุคลากรจำเป็นต้องเปลี่ยนแปลง การมีตัวแทนฝ่ายทรัพยากรบุคคลในทีมอาจเป็นประโยชน์
ทีม 8D ควรมีสมาชิกหลักสองคน:
- ผู้นำ: คือบุคคลที่รู้กระบวนการ 8D และสามารถแนะนำทีมผ่านขั้นตอนนั้นได้ (แม้ว่าจะไม่ใช่บุคคลที่รู้มากที่สุดเกี่ยวกับปัญหาที่กำลังศึกษาอยู่ก็ตาม)
- Champion : คือบุคคลที่สามารถให้การอนุมัติขั้นสุดท้ายของการเปลี่ยนแปลงที่จะนำไปใช้โดยใช้วิธี 8D
กำหนดปัญหา
ปัญหาจะต้องถูกกำหนดโดยใช้เงื่อนไขเชิงปริมาณ การร้องเรียนของลูกค้าอาจเป็น: “ผลิตภัณฑ์นี้ใช้งานไม่ได้!” » แต่ภายในองค์กรจะต้องอธิบายปัญหาอย่างแม่นยำและเป็นตัวเลข
การระบุปัญหาอาจต้องมีการกำหนดวิธีการทดสอบและการรวบรวมข้อมูล การสัมภาษณ์ลูกค้า หรือการพูดคุยกับพนักงานที่เกี่ยวข้องกับการผลิตผลิตภัณฑ์
ณ จุดนี้ ทีมงานไม่ได้มองหาสาเหตุของปัญหา แต่รวบรวมข้อมูลให้ได้มากที่สุดเพื่อระบุลักษณะของปัญหา
ใช้มาตรการกักกันชั่วคราว
หากปัญหาส่งผลกระทบต่อลูกค้า ส่งผลกระทบต่อประสิทธิภาพการผลิตหรือต้นทุน หรือสร้างความเสี่ยงด้านสุขภาพหรือสิ่งแวดล้อม จะต้องได้รับการแก้ไขทันที ต้องมีการระบุ ประเมิน และดำเนินการแก้ไขปัญหาชั่วคราว
หากไม่สามารถแก้ไขปัญหาชั่วคราวได้ จำเป็นต้องหยุดหรือปิดกระบวนการที่มีปัญหา
โปรดทราบว่าไม่ควรใช้วิธีแก้ปัญหาชั่วคราวโดยไม่มีการประเมินล่วงหน้า ทีมงานต้องตรวจสอบให้แน่ใจว่าวิธีแก้ปัญหามีความปลอดภัย แก้ไขปัญหาปัจจุบันได้จริง และนำไปปฏิบัติได้ง่ายและคุ้มต้นทุน โดยไม่ก่อให้เกิดปัญหาใหม่
ระบุสาเหตุที่แท้จริง
เมื่อแก้ไขปัญหาได้แล้ว ขั้นตอนต่อไปคือการระบุสาเหตุของปัญหา เป้าหมายโดยรวมของวิธี 8D คือการกำจัดปัญหาอย่างถาวร และสามารถทำได้ก็ต่อเมื่อมีการระบุและกำจัดสาเหตุที่แท้จริงแล้วเท่านั้น
เครื่องมือต่อไปนี้อาจมีประโยชน์ในขั้นตอนนี้:
กำหนดการดำเนินการแก้ไข
เมื่อเราทราบสาเหตุของปัญหาแล้ว เราจำเป็นต้องค้นหาและดำเนินการเพื่อแก้ไขปัญหา สิ่งสำคัญคือการดำเนินการแก้ไขจะแก้ไขที่ต้นตอของปัญหา เพราะหากไม่ระบุสาเหตุที่แท้จริงของปัญหา ปัญหาก็จะเกิดขึ้นอีก
หนึ่งในวิธีที่ดีที่สุดในการทดสอบโซลูชันคือการนำไปใช้ในขนาดเล็กและติดตามสิ่งที่เกิดขึ้น ตัวอย่างเช่น หากกระบวนการผลิตเกี่ยวข้องกับหลายเซลล์ โซลูชันสามารถนำไปใช้ในเซลล์เดียว จากนั้นจึงวัดผลลัพธ์ที่ได้รับ หากการแก้ปัญหาสำเร็จในเซลล์เดียว ก็สามารถนำไปปฏิบัติในทุกเซลล์ได้
ดำเนินการแก้ไขอย่างถาวร
เมื่อตรวจสอบแนวทางแก้ไขแล้ว นั่นคือ ได้รับการพิสูจน์แล้วว่าสามารถขจัดต้นเหตุได้โดยไม่สร้างปัญหาใหม่ให้สามารถนำไปใช้ได้เต็มที่โดยใช้มาตรการถาวร
เพื่อให้การเปลี่ยนแปลงถาวรประสบความสำเร็จ จำเป็นอย่างยิ่งที่จะต้องวางแผนว่าการเปลี่ยนแปลงจะถูกนำมาใช้อย่างไร แผนโครงการควรครอบคลุมถึง: วิธีการสื่อสารการเปลี่ยนแปลงกับทุกคนที่เกี่ยวข้อง สิ่งที่ต้องดำเนินการ และวิธีติดตามการเปลี่ยนแปลง
ป้องกันไม่ให้ปัญหาที่คล้ายกันเกิดขึ้นอีก
การแก้ปัญหาโดยสมบูรณ์หมายถึงการป้องกันไม่ให้ปัญหาเกิดขึ้นอีก ดังนั้นตามวิธี 8D ควรใช้มาตรการป้องกันเพื่อป้องกันไม่ให้ปัญหาเกิดขึ้นอีก ซึ่งเกี่ยวข้องกับการทบทวนกระบวนการจัดการ ขั้นตอนการปฏิบัติงาน และคู่มือการฝึกอบรมเพื่อให้แน่ใจว่ามีการปฏิบัติตามแนวทางปฏิบัติที่ดีที่สุด
ในขั้นตอนนี้ องค์กรควรพิจารณาการดำเนินการต่างๆ รวมถึงการอัปเดตคำถามการตรวจสอบกระบวนการ และตรวจสอบเป็นประจำกับการดำเนินการแก้ไขเพื่อลดความเสี่ยงในกระบวนการอื่นๆ
วิธีการที่ใช้กันอย่างแพร่หลายในการป้องกันปัญหาไม่ให้เกิดขึ้นคือ โพคาแอก อย่างไรก็ตาม ในบางกรณีอาจเป็นเรื่องยากที่จะนำวิธีนี้ไปใช้ คุณสามารถดูว่าโพก้าแอกคืออะไรโดยคลิกที่ลิงค์ต่อไปนี้:
รับรู้ถึงความพยายามของทีม
การตระหนักถึงความสำเร็จของทีมเป็นขั้นตอนสุดท้ายของวิธี 8D มันอาจจะง่ายพอๆ กับการ “ขอบคุณ” แต่ควรทำในลักษณะที่คนอื่นๆ ในองค์กรของคุณรู้ว่าได้ทำอะไรไปบ้าง สิ่งนี้จะเพิ่มความพึงพอใจและแรงจูงใจของผู้ที่เป็นส่วนหนึ่งของทีมและทำงานอย่างหนักเพื่อค้นหาวิธีแก้ไขปัญหา
วิธีแสดงความขอบคุณโดยทั่วไปคือการติดบทความในจดหมายข่าวของบริษัทหรือติดป้ายบนกระดานข่าวของสถานที่ ตรวจสอบให้แน่ใจว่าสมาชิกในทีมทุกคนได้รับการตั้งชื่อเพื่อให้ทุกคนได้รับการยอมรับว่าเป็นส่วนหนึ่งของทีม
ตัวอย่างวิธี 8D
หลังจากที่ได้เห็นทฤษฎีเกี่ยวกับวิธี 8D แล้ว เราจะเห็นตัวอย่างการประยุกต์ใช้วิธี 8D ในการแก้ปัญหาด้านคุณภาพของบริษัทอุตสาหกรรม
องค์กรแห่งหนึ่งได้รับการร้องเรียนจากลูกค้าเกี่ยวกับการหดตัวของชิ้นส่วนรถยนต์ ฝ่ายบริหารจำเป็นต้องมีการวิเคราะห์เชิงลึกโดยอิงตามวิธีการแก้ปัญหา 8D รายงาน 8D ที่ส่งมีดังนี้:
- D1: มีการจัดตั้งทีมขึ้นโดยประกอบด้วยสมาชิกในทีมจัดซื้อ หัวหน้าทีม และผู้จัดการ
- D2: มีการใช้คำร้องเรียนจากลูกค้าเพื่ออธิบายปัญหา ปัญหาเกิดขึ้นโดยการตอบคำถามต่อไปนี้:
- มีการร้องเรียนอะไร? การหดตัวในอ่างล้างจาน
- มันเกิดขึ้นเมื่อไร? ในชุดสุดท้าย.
- ทำไมสิ่งนี้ถึงเกิดขึ้น? เนื่องจากมีข้อบกพร่องในกล่องอินพุต
- ใครแจ้งปัญหา? ลูกค้าปลายทาง
- การผลิตเกี่ยวข้องกับอะไร? 2% ของการผลิตทั้งหมด
- D3: เพื่อเป็นมาตรการกักกัน ทีมงานจึงตัดสินใจหยุดจัดส่งและแยกชิ้นส่วนที่ดีออกทันที
- D4: เพื่อระบุสาเหตุที่แท้จริง ทีมงานใช้วิธีการ 5 Whys:
- ทำไมพวกเขาถึงบ่น? โดยการหดตัวในโซนทางเข้า
- เหตุใดบริเวณทางเข้าจึงแคบลง? เนื่องจากใช้อุณหภูมิในการหล่อสูง
- เหตุใดจึงใช้อุณหภูมิการหล่อสูง? เนื่องจากการอ่านค่าไพโรมิเตอร์ไม่ถูกต้อง
- เหตุใดค่าไพโรมิเตอร์จึงอ่านไม่ถูกต้อง เนื่องจากไม่ได้ตรวจสอบสภาพของไพโรมิเตอร์
- เหตุใดจึงไม่ตรวจสอบไพโรมิเตอร์ สรุปได้ว่าต้นตอของปัญหาคือไพโรมิเตอร์อยู่ในสภาพที่ไม่ดี
- D5: ตามแผนแก้ไขถาวร แนะนำให้หัวหน้างานบำรุงรักษาแก้ไขไพโรมิเตอร์เป็นระยะ
- D6: มีการดำเนินการแก้ไขอย่างถาวรและมีการกำหนดการตรวจสอบรายสัปดาห์
- D7: การตรวจสอบเป็นระยะและการบำรุงรักษาไพโรมิเตอร์อย่างเหมาะสมเป็นการดำเนินการเพื่อป้องกันปัญหาไม่ให้เกิดขึ้นอีก
- D8: ความพยายามของทีมได้รับการยอมรับ ขอชื่นชมผู้จัดการและทีมงานในการแก้ไขปัญหานี้
เมื่อใดจึงควรใช้วิธี 8D?
โดยทั่วไปแล้ว วิธีการแก้ไขปัญหาแบบ 8D จะใช้เมื่อเกิดสถานการณ์ใดสถานการณ์หนึ่งต่อไปนี้:
- เมื่อพบปัญหาที่เกี่ยวข้องกับความปลอดภัยหรือไม่เป็นไปตามกฎระเบียบหรือกฎเกณฑ์ใดๆ
- เมื่อได้รับการร้องเรียนจากลูกค้า ในส่วนก่อนหน้านี้ คุณสามารถดูตัวอย่างวิธีการใช้วิธี 8D ในกรณีนี้ได้
- เมื่อได้รับการแจ้งเตือนว่าอัตราความล้มเหลวของผลิตภัณฑ์สูงกว่าที่คาดไว้
- เมื่อผลิตภัณฑ์มักจะไม่ผ่านการทดสอบคุณภาพภายใน จะมีการปล่อยหน่วยมากเกินไปหรือประสิทธิภาพของผลิตภัณฑ์หรือบริการต่ำมาก
ข้อดีของวิธี 8D
การใช้วิธี 8D ในการจัดการคุณภาพมีข้อดีดังต่อไปนี้:
- โดยมีขั้นตอนง่ายๆ ในการแก้ไขปัญหาและค้นหาสาเหตุที่แท้จริง
- ซึ่งจะช่วยในการค้นหาวิธีแก้ไขปัญหาและนำไปปฏิบัติให้สำเร็จเพื่อไม่ให้ปัญหาเกิดขึ้นอีก
- ทำให้ง่ายต่อการค้นหาระบบควบคุมที่ไม่สามารถตรวจพบปัญหาจึงจำเป็นต้องปรับปรุง
- ในทางตรรกะสิ่งนี้จะช่วยปรับปรุงคุณภาพของผลิตภัณฑ์หรือบริการซึ่งนำไปสู่ความพึงพอใจของลูกค้าทางอ้อมมากขึ้น
- สิ่งนี้ส่งเสริมการทำงานเป็นทีม เนื่องจากพนักงานที่ประกอบเป็นทีมจะต้องทำงานร่วมกันเพื่อแก้ไขปัญหา