Méthode 8D (qualité)
Cet article explique ce qu’est la méthode 8D et à quoi elle sert. Ainsi, vous découvrirez quelles sont les huit étapes de la méthode 8D, un exemple de son application et quels sont les avantages de mettre en œuvre cette méthodologie en entreprise.
Qu’est-ce que la méthode 8D ?
La méthode 8D , également appelée huit disciplines de résolution de problèmes , est un modèle utilisé pour résoudre des problèmes de gestion de la qualité. La méthode 8D comprend huit étapes qui doivent être suivies pour résoudre le problème, le corriger et éliminer sa cause.
Ainsi, la méthode 8D repose sur l’application d’une action corrective permanente basée sur l’analyse statistique du problème et de l’origine du problème en déterminant les causes profondes.
La méthode 8D est également appelée sous d’autres noms tels que Résolution de problèmes 8-D , G8D ou Global 8D .
La méthode de résolution de problèmes de qualité 8D a été inventée par le constructeur automobile Ford en 1987. À l’époque, l’entreprise appelait cette méthodologie G8D ou Global 8D. Actuellement, la méthode 8D n’est pas seulement utilisée par les entreprises du secteur automobile, mais également dans d’autres industries pour résoudre des problèmes liés à la gestion de la qualité.
La méthode 8D est similaire à la méthode PDCA dans la mesure où toutes deux fournissent une procédure pour résoudre un problème et améliorer la qualité d’un produit, d’un processus ou d’un service. Vous pouvez voir les similitudes et les différences entre ces deux méthodologies ici :
Que sont les 8D ?
En management de la qualité, les huit disciplines de la méthode 8D sont :
- D1 : Formez une équipe.
- D2 : Définir le problème.
- D3 : Mettre en œuvre une action de confinement provisoire.
- D4 : Identifiez la cause profonde.
- D5 : Déterminer les actions correctives.
- D6 : Mettre en œuvre des actions correctives permanentes.
- D7 : Evitez qu’un problème similaire ne se reproduise.
- D8 : Reconnaître les efforts de l’équipe.
Remarque : Bien que la méthode 8D comportait initialement huit étapes, certains experts en qualité ajoutent désormais une étape initiale appelée Actions de préparation et d’intervention en cas d’urgence .
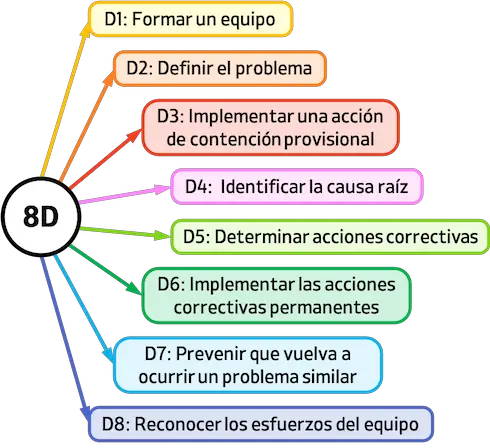
Faire une équipe
L’équipe doit être multidisciplinaire et inclure une expérience dans le produit, le processus ou le service étudié. En cas de problème avec un produit, il est essentiel de comprendre les besoins du client. Il est donc utile d’avoir un représentant marketing ou même un client dans l’équipe. De même, lorsque les processus et le personnel doivent changer, il peut être utile d’avoir un représentant des ressources humaines dans l’équipe.
Les équipes 8D doivent avoir deux membres clés :
- Leader : est la personne qui connaît le processus 8D et peut guider l’équipe à travers celui-ci (même si ce n’est pas toujours celui qui connaît le plus le problème étudié).
- Champion : est la personne qui peut donner l’approbation finale des changements à mettre en œuvre en utilisant la méthodologie 8D.
définir le problème
Le problème doit être défini en utilisant des termes quantifiables. La plainte du client peut être : « Ce produit ne fonctionne pas ! » mais en interne, l’organisation doit décrire le problème de manière précise et numérique.
Définir le problème peut nécessiter l’établissement de méthodes de test et la collecte de données, des entretiens avec des clients ou des discussions avec des travailleurs impliqués dans la fabrication du produit.
À ce stade, l’équipe ne cherche pas la cause du problème, mais plutôt de rassembler le plus d’informations possible pour déterminer les caractéristiques du problème.
Mettre en œuvre des mesures de confinement provisoires
Si le problème affecte les clients, a un impact sur la productivité ou les coûts, ou crée un risque pour la santé ou l’environnement, il doit être résolu immédiatement. Une solution temporaire doit être identifiée, évaluée et mise en œuvre.
Si une solution temporaire n’est pas réalisable, il sera nécessaire d’arrêter ou de fermer le processus qui pose problème.
Gardez à l’esprit qu’une solution temporaire ne doit pas être mise en œuvre sans évaluation préalable. L’équipe doit s’assurer que la solution de contournement est sécurisée, qu’elle résout réellement le problème actuel et qu’elle est facile et rentable à mettre en œuvre, sans provoquer de nouveaux problèmes.
Identifier la cause profonde
Une fois la solution de contournement en place, l’étape suivante consiste à identifier la cause première du problème. L’objectif global de la méthode 8D est d’éliminer définitivement le problème et cela ne peut être fait que si la cause profonde est identifiée et éliminée.
Les outils suivants peuvent être utiles à ce stade :
Déterminer les actions correctives
Une fois que nous connaissons la cause profonde du problème, nous devons trouver et mettre en œuvre des actions qui résolvent le problème. Il est important que les actions correctives s’attaquent à la cause profonde du problème, car si la véritable cause du problème n’est pas résolue, le problème se reproduira.
L’un des meilleurs moyens de tester une solution est de la mettre en œuvre à petite échelle et de surveiller ce qui se passe. Par exemple, si un processus de fabrication implique plusieurs cellules, la solution peut être mise en œuvre dans une seule cellule puis mesurer les résultats obtenus. Si la solution réussit dans une cellule, elle peut ensuite être mise en œuvre dans toutes les cellules.
Mettre en œuvre des actions correctives permanentes
Une fois que la solution a été vérifiée, c’est-à-dire qu’il a été prouvé qu’elle éliminera la cause profonde sans créer de nouveaux problèmes, elle peut être pleinement mise en œuvre en prenant des mesures permanentes.
Pour réussir la mise en œuvre d’un changement permanent, il est essentiel de planifier la manière dont le changement sera mis en œuvre. Le plan de projet doit couvrir : comment le changement sera communiqué à toutes les personnes concernées, quelles mesures doivent être prises et comment le changement sera surveillé.
Empêcher qu’un problème similaire ne se reproduise
Une solution complète aux problèmes signifie empêcher qu’ils ne se reproduisent. Ainsi, selon la méthode 8D, des mesures préventives doivent être mises en œuvre pour éviter que le problème ne se reproduise, cela implique de revoir les processus de gestion, les procédures opérationnelles et les manuels de formation pour s’assurer que les meilleures pratiques sont suivies.
À ce stade, les organisations doivent envisager des actions, notamment la mise à jour des questions d’audit des processus et leur vérification régulière par rapport aux actions correctives afin de réduire les risques dans d’autres processus.
Une méthode largement utilisée pour éviter que des problèmes ne surviennent est le poka-yoke, cependant, dans certains cas, il peut être difficile d’appliquer cette méthodologie. Vous pouvez voir en quoi consiste un poka-yoke en cliquant sur le lien suivant :
Reconnaître les efforts de l’équipe
Reconnaître les réalisations de l’équipe est la dernière étape de la méthode 8D. Il peut s’agir d’un simple « merci », mais cela doit être fait de manière à ce que les autres membres de votre organisation sachent ce qui a été fait. Cela augmente la satisfaction et la motivation des personnes qui faisaient partie de l’équipe et qui ont travaillé si dur pour trouver une solution au problème.
Une façon courante de dire merci consiste à publier un article dans le bulletin d’information de l’entreprise ou à afficher une bannière sur les tableaux d’affichage de l’établissement. Assurez-vous que tous les membres de l’équipe sont nommés afin que chacun soit reconnu comme faisant partie de l’équipe.
Exemple de la méthode 8D
Après avoir vu la théorie sur la méthode 8D, nous allons voir un exemple d’application de la méthode 8D résolvant un problème de qualité d’une entreprise industrielle.
Une organisation a reçu des plaintes de clients concernant le rétrécissement d’une pièce automobile. La direction a exigé une analyse approfondie basée sur la méthodologie de résolution de problèmes 8D. Le rapport 8D envoyé était le suivant :
- D1 : Une équipe est constituée avec les membres de l’équipe approvisionnement, le chef d’équipe et le manager.
- D2 : Une réclamation client est utilisée pour décrire le problème. Le problème est établi en répondant aux questions suivantes :
- Quelle est la plainte ? Contraction dans l’évier.
- Quand est-ce arrivé? Dans le dernier lot.
- Pourquoi est-ce arrivé ? En raison d’un défaut dans la zone de saisie.
- Qui a signalé le problème ? Un client final.
- Quelle est la production concernée ? 2% de la production totale.
- D3 : En guise de mesure de confinement, l’équipe décide d’arrêter les expéditions et de séparer immédiatement les bonnes pièces.
- D4 : Pour identifier la cause profonde, l’équipe utilise la méthodologie des 5 Pourquoi :
- Pourquoi se sont-ils plaints ? Par une contraction dans la zone d’entrée.
- Pourquoi y a-t-il eu un rétrécissement dans la zone d’entrée ? Parce que des températures de coulée élevées ont été utilisées.
- Pourquoi des températures de coulée élevées ont-elles été utilisées ? Parce que la lecture du pyromètre était incorrecte.
- Pourquoi la lecture du pyromètre était-elle incorrecte ? Parce que l’état du pyromètre n’a pas été vérifié.
- Pourquoi l’état du pyromètre n’a-t-il pas été vérifié ? Il est conclu que la cause première du problème est que le pyromètre était en mauvais état.
- D5 : Comme plan correctif permanent, il est suggéré au superviseur de maintenance de réviser périodiquement le pyromètre.
- D6 : Des actions correctives permanentes sont mises en œuvre et des contrôles hebdomadaires sont programmés.
- D7 : Une inspection périodique et un entretien approprié des pyromètres sont des actions permettant d’éviter que le problème ne se reproduise.
- D8 : L’effort d’équipe est reconnu. Le manager et l’équipe sont félicités pour avoir résolu le problème.
Quand appliquer la méthode 8D ?
En général, la méthode 8D de résolution de problèmes est utilisée lorsque l’une des situations suivantes se produit :
- Lorsque des problèmes liés à la sécurité sont découverts ou qui ne sont conformes à aucune réglementation ou réglementation.
- Lorsque les plaintes des clients sont reçues. Dans la section précédente, vous pouvez voir un exemple de la façon d’implémenter la méthode 8D dans ce cas.
- Lorsque des alertes sont reçues indiquant que le taux de défaillance du produit est plus élevé que prévu.
- Lorsque les produits ne passent souvent pas les tests de qualité internes, trop d’unités sont jetées ou les performances du produit ou du service sont très faibles.
Avantages de la méthode 8D
La mise en œuvre de la méthode 8D dans la gestion de la qualité présente les avantages suivants :
- Il fournit une procédure simple pour résoudre un problème et trouver sa cause profonde.
- Cela aide à trouver une solution au problème et à la mettre en œuvre avec succès afin que le problème ne se reproduise plus.
- Cela permet de trouver facilement les systèmes de contrôle qui n’ont pas pu détecter le problème et qui doivent donc être améliorés.
- Logiquement, cela améliore la qualité du produit ou du service, ce qui entraîne indirectement une plus grande satisfaction des clients.
- Cela encourage le travail d’équipe, puisque les travailleurs qui composent l’équipe doivent travailler ensemble pour résoudre le problème.